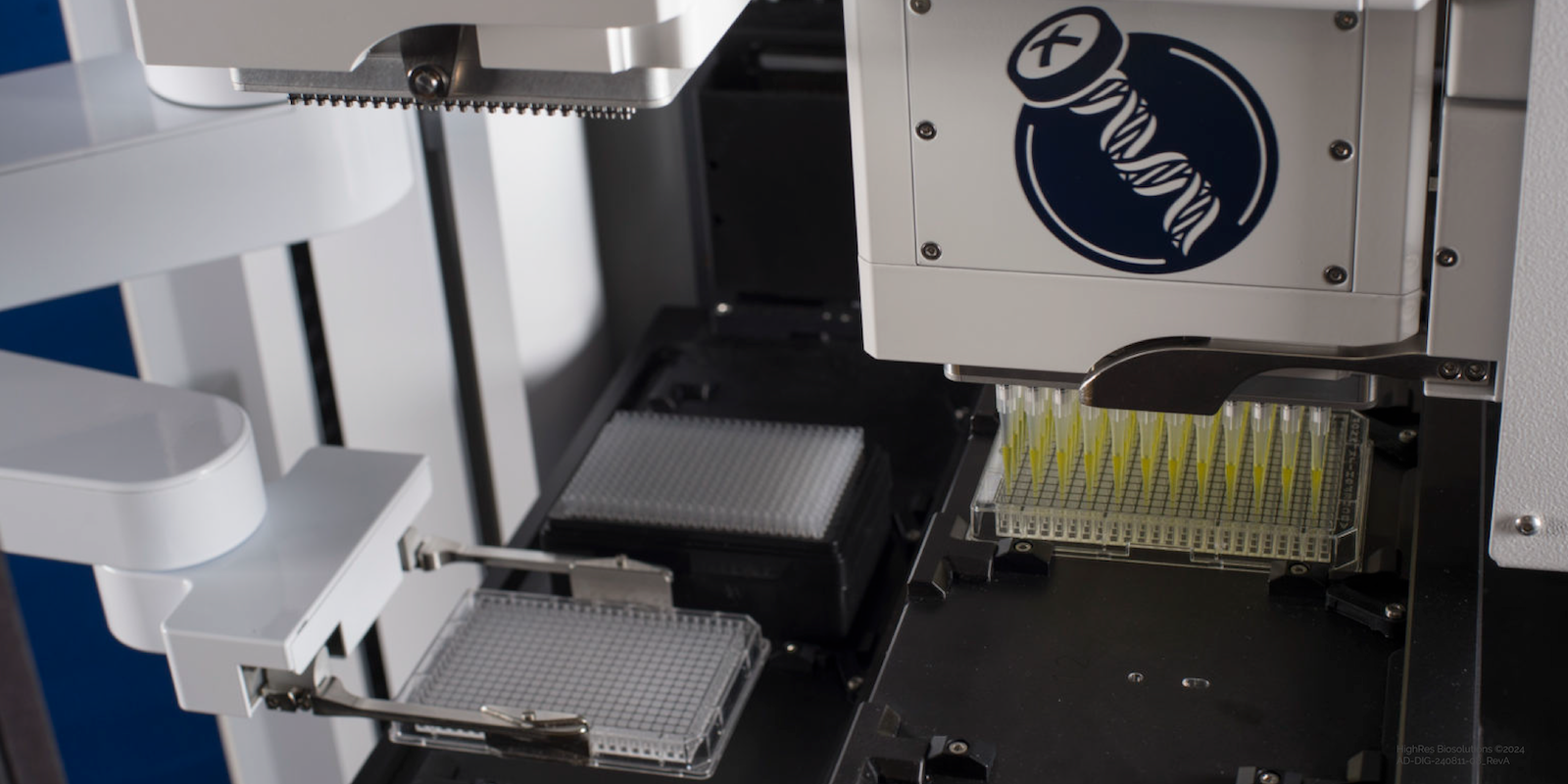
High-Density Microplates Continue to Gain Popularity
High-density plate formats, including 384- and 1536-well plates, continue to gain popularity in many research applications. In contrast to tube-based assays and lower-density plates, high-density microplates are seen as a principle means of reducing experimental costs. In addition to offering more sample throughput within a given period, these plates enable assay miniaturization to decrease reagent and sample consumption.
While automated liquid handling technologies are known to process 96-well plates with ease, the progression into 384-well and 1536-well microplates is more challenging. The wells of these plates are much smaller than those found in a 96-well plate configuration, so pipetting head and tip alignment require extreme accuracy and repeatability.
To facilitate pipetting in 384- and 1536-well formats, automated liquid handlers rely on several capabilities, including core instrument alignment, robust component use, and high accuracy gantry robots. However, one of the most essential elements to consider when evaluating automated liquid handlers is the nest design.
The Role of Nest Design in Automated Liquid Handlers
In the world of automated liquid handlers, a nest is any location where a microplate is placed. This could be a temporary position as a robotic arm places a plate on a deck and the liquid handler’s gripper moves the plate to a different on-deck location. It could also be the location where liquid transfers take place.
Even when using high quality and precise automated equipment and components, there is typically room for location variation between a microplate and a standard plate nest. Location variation means that the plate has a slight amount of wiggle room in the nest.
Nest Location Variations Impact Pipetting
When transferring liquids to and from a 96-well plate, this variation is usually inconsequential. Tips on the liquid handler’s pipetting head can align easily with the relatively large wells.
On the other hand, when using a 384- or 1536-well plate, the wells in these formats are so small that even the smallest variation of plate location in the nest may be more than the reasonable accuracy and repeatability tolerances. Misaligned tips on a 96 or 384 channel pipetting head may not dispense properly (if at all) into the wells, which can jeopardize the entire assay.
Overcoming Nest Location Variation
Fortunately, the issue of precise plate location within the nest is not difficult to overcome. Mechanical locating elements can repeatedly guide plates to a fixed position. These elements can be passive or active.
Passive positioning relies on an element, such as a spring or clip, that presses against a microplate to prevent plate movement in the nest. The resistance created by the spring or clip may present a slight challenge for collaborative robots as they seat the microplate in the nest.
Active plate positioning in a nest is achieved with a cam-actuated mechanism. When a microplate is placed into the nest, the mechanism engages multiple locating guides to position the plate precisely and securely. The guides are disengaged easily when the plate is removed from the nest for smooth workflow transitions.
These locating elements significantly reduce or eliminate the plate-to-nest location error margin to ensure proper workflow performance, protect data integrity, and prevent time-consuming delays due to mechanical issues or the need to rework samples.
Locating Nests in Your Automated Workflow
When purchasing an automated liquid handler, many manufacturers offer locating mechanics in the nests as optional add-ons for an additional fee. To counter these fees, many users settle for decks outfitted with a mix of locating and non-locating nests.
This mix may constrain how protocols are designed as well as sample throughput potential. For example, if you are working with 1536-well plates, and your 84-position deck only features two locating nests, then you effectively have a 2-position liquid handler as any non-locating nests will have too much play for precise positioning and pipetting.
By contrast, the Prime automated liquid handler features active locating as standard features on all ten nests among its two dynamic trays. The ten locating nests perform in a manner that offers nearly limitless nest supply. As labware is loaded on one dynamic tray, the other tray is used by the pipetting head to aspirate and dispense into microplates with densities as high as 1536 wells. By loading and unloading in parallel to core liquid handling functions, you can increase throughput and decrease active hands-on time.
If your workflow plans include high density microplate formats, it is important to consider the number and configuration of locating nests on your liquid handling deck thoughtfully.
Contact our automation experts at sales@highresbio.com today to learn how active locating nests can improve your high-density microplate processing workflows.
Revision: BL-DIG-190131-01_RevC