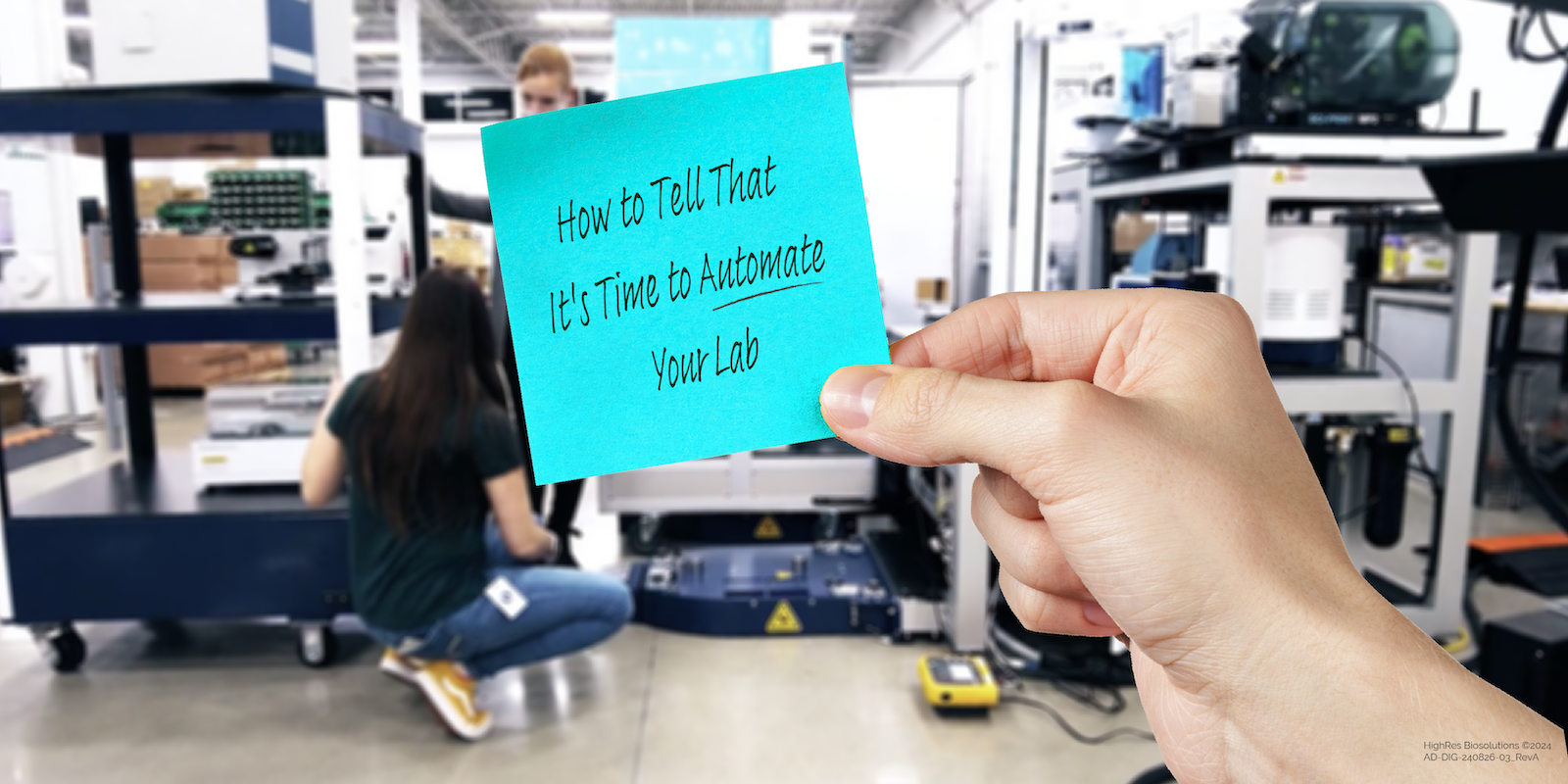
Today’s Pressure to Produce
The pace of scientific research and subsequent publications over the past years increased with the onset of the COVID-19 pandemic. As this trend continues, it will pressure academic and industry experts alike to expand their research and development capabilities.
As one of these experts, you may already feel pressured by the complexity of managing and operating a laboratory. And with so many moving parts to manage and track, it can be difficult to recognize and prioritize when to change long-standing workflows and processes.
Whether your focus is small or large molecule entity research, gene therapy development, recombinant virus production, or more, you may be contemplating questions related to the progression of your lab. How do you ease the team’s current pain points and bottlenecks? How do you improve sample uniformity across the multitude of assays being performed in the lab? Is the lab experiencing temporary roadblocks or symptoms of underlying issues in current processes.
Automation as a Solution
When it comes to addressing production hurdles and improving lab output, few tools are as impactful as laboratory automation. Automated solutions can alleviate workflow constraints among team members. Additionally, they can empower the team to automate simple tasks today and, as research expands over time, evolve the automated solution to meet the future demands of your science and organization.
At HighRes Biosolutions, we have decades of experience helping customers, from small labs to large multi-national organizations, to streamline and enhance their lab operations and workflows. Below are the most common signs that we’ve seen over the years that a lab is outgrowing its current workflows and ready for automation.
#1. Expanding Sample Consumption
Over the past seven years, we have seen a market trend toward smaller and more focused assays. Though these focused assays may require fewer samples to be processed, labs may counter this by increasing the number of workflows in operation simultaneously. More assays mean increased sample consumption and increased workload demand on the lab members. Stress from the increased workload can contribute to errors and false positives.
If this is occurring in your lab, take the time to compile and analyze the commonly repeated tasks and recurring errors. If your data indicates an increase in errors due to repeatable tasks, then it may be time to evaluate and implement automation across your lab. A fully automated system can process samples in parallel and can also instantly scale to handle increased demand without sacrificing data quality.
#2. Inconsistent Experimental Results
As your team’s assay workload increases, you may encounter varying test results along with sample uniformity issues. This could signal that your team is struggling to keep pace with research demand.
Inconsistency can be incredibly detrimental to your operations, as precision is critical when measuring lab performance. One of the single largest contributors to lab inconsistency is human error. This is easy to understand in the context of all the responsibilities of a lab analyst.
Performing manual preparation of tens of thousands of samples by hand can be a laborious and tedious process. It can be quite challenging to maintain a consistent level of accuracy while performing these tasks manually. Thankfully, lab automation can convert these manual tasks into automated workflows that can complete the tasks rapidly and with a high degree of accuracy and consistency.
Another common inconsistency comes from samples that experience varying experimental conditions as analysts try to scale up work production. Batching often leads to protracted wait or treatment times and the resulting data are sometimes difficult to reproduce. Parallel processing presents its own set of challenges. It is therefore vital that the automation software you choose to oversee your automated laboratory ecosystem is adaptable and scalable.
#3. High Labor Costs
A crystal-clear sign that it’s time to automate your lab is labor cost, typically the largest fixed expense for any lab. Labor costs that are too high can throw off the careful balance of staff resources, equipment, lab supplies, and other important variables in a typical lab budget.
Lab automation can be a cost-saving solution if your lab is consistently overspending on labor. These hands-free systems can run and operate with minimal human supervision, and an automated workflow can facilitate an increased number of experiments in the lab while minimizing full-time employee (FTE) labor costs. The cost savings realized in the long term from automated workflows can be tremendous.
Types of Laboratory Automation
Once you’ve made the decision to bring automation into your lab, the next step is to determine what type of automated solution is ideal for your needs. Several laboratory automation types are available, each with its own benefits and applications. These include:
- Pre-Analytical Automation – Automating the process involved in sample collection, transportation, and processing. Examples include automated sample handling and sorting, automated labeling, and automated transport systems.
- Analytical Automation – Automating sample analysis. Examples include automated liquid handling and automated systems that can perform multiple tests simultaneously.
- Post-Analytical Automation – Automating reporting and data management. Examples include automated result reporting, data entry, and interfacing with electronic health records.
- Total Laboratory Automation (TLA) – Integrating all aspects of laboratory automation—from sample handling to result reporting—in a single, seamless system. This can improve laboratory efficiency, reduce errors, and streamline workflows.
In addition to these types, some automated systems come in different configurations, from simple to complex depending on your lab needs and workflow requirements. Modular solutions, like our Nucleus automation infrastructure, allow you to purchase the system to suit your requirements now, and change or update at any time in the future as your requirements change.
When is The Right Time to Automate Your Lab?
Only you and your team know for sure when it’s time to automate your lab. However, if you’re experiencing issues with results consistency, difficult to manage spikes in assay demand, or increased labor costs, it might be time to implement automation.
Lab automation can expedite work in various application areas such as compound management, high throughput screening, cell culture, cell-based and biochemical assays, genomics, and more. It doesn't matter where you start, HighRes Biosolutions possesses the proficiency and knowledge to assist you in starting your automation journey on the right path.
As one of the most experienced lab automation partners in the industry, our engineers, developers, and automation specialists work closely with you to develop solutions that bring measurable results and improved productivity to your workflows. We invite you to connect with us so that we can better understand your needs and assist in your automation project.
Revision: BL-DIG-210930-01_RevC