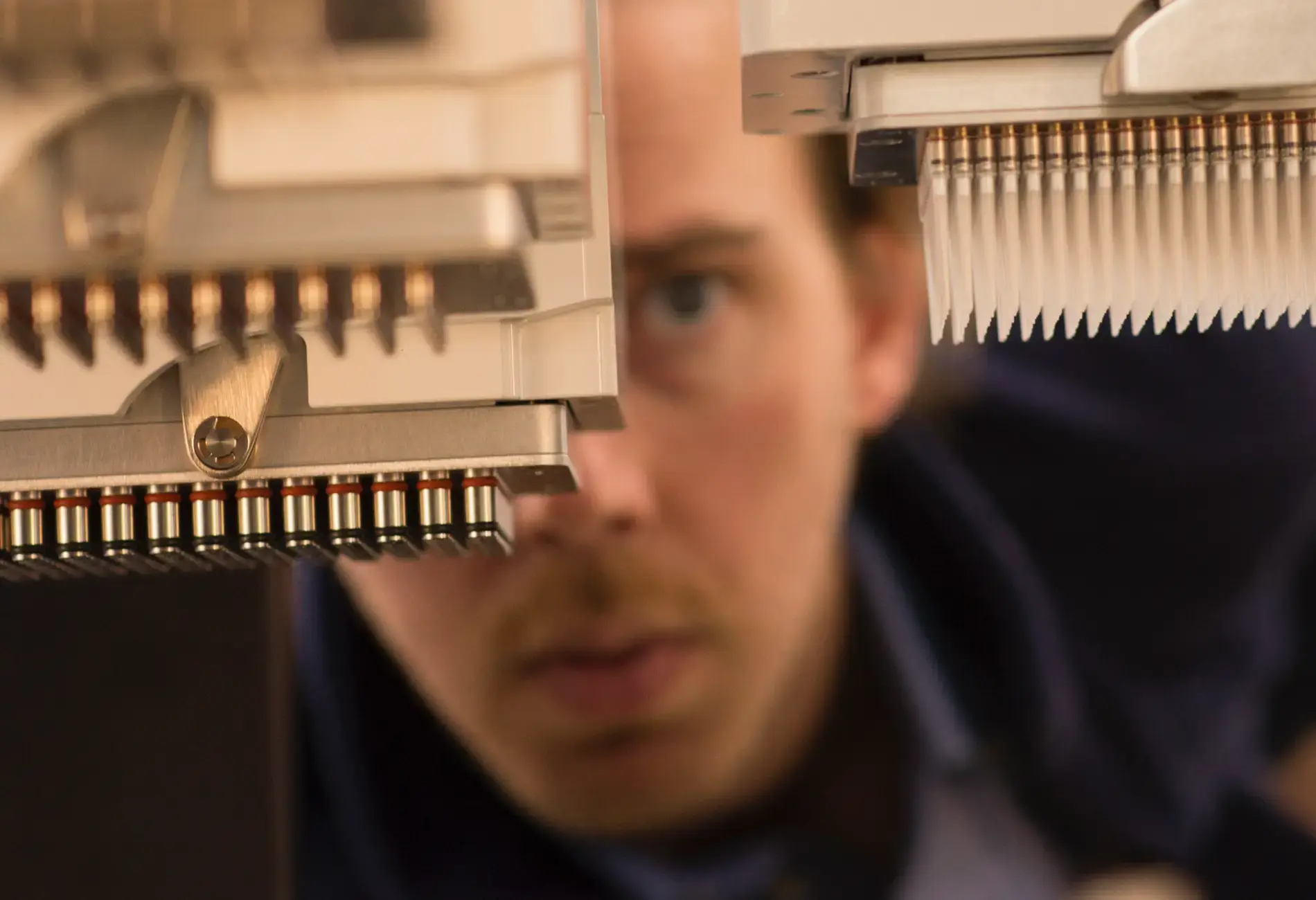
Liquid handling systems that reliably and repeatably manipulate liquids down to microliter quantities are a key tool in the modern laboratory. Therefore, understanding liquid handling is crucial for optimizing laboratory workflows and enhancing research outcomes in various scientific disciplines.
How Liquid Handlers Work
Liquid handlers, both manual and automated, operate by accurately measuring and transferring liquids. These systems comprise components like pipettes, dispensers, and mixers, integrated with technology to ensure precision and control. Automated systems further incorporate robotics and software for higher throughput applications or to increase repeatability when higher levels of control are needed. Additionally, automated liquid handling can significantly reduce the potential for human error in repetitive tasks.
Key Techniques in Liquid Handling
Pipetting
Pipetting is a fundamental technique in liquid handling, involving drawing a liquid into a pipette and dispensing it into a destination vessel. This technique is crucial for tasks such as sample preparation, dilution, and transfer of reagents. Accurate pipetting ensures that the volumes of liquid handled are precise, which is vital for the reproducibility of experimental results. There are various types of pipettes, including manual, electronic, and multi-channel pipettes, each suited to different applications and volume ranges.
Dispensing
Dispensing involves delivering a liquid in a controlled manner, often used in assays and reagent addition. It is key to ensuring consistent experimental conditions, particularly in high-throughput screening and quantitative assays. Dispensers can range from simple manual devices to sophisticated automated systems capable of handling multiple reagents simultaneously. The precision of dispensing directly impacts the reliability and consistency of the results obtained from experimental procedures.
Mixing
Mixing is the process of combining two or more liquids to achieve a homogeneous solution. This step is essential in reagent preparation, sample homogenization, and biochemical reactions. Effective mixing ensures that all components are uniformly distributed, which is critical for the accuracy of downstream procedures or analyses. Mixing can be achieved using various methods, including vortexing, stirring with magnetic bars, and using automated mixing systems that are integrated into automated liquid handlers.
Principle of Liquid Handling Systems
Liquid handling systems operate on principles of fluid dynamics, ensuring accuracy and precision in handling liquids that possess different physical properties. Factors such as viscosity, volatility, and surface tension must all be considered to ensure reliable and repeatable liquid transfer. Liquid handling systems are designed to minimize the risk of cross-contamination and evaporation, which can significantly affect the integrity of both samples and reagents. Advanced liquid handling systems often incorporate sensors and feedback mechanisms to monitor and adjust parameters in real-time, enhancing their reliability and performance.
Calibration and Maintenance
Calibration and maintenance are vital to ensuring the accuracy of liquid handling devices. Regular gravitation and volumetric calibration checks verify that liquid handling equipment is dispensing the correct volumes, while maintenance tasks, such as cleaning and replacing worn parts, help maintain system performance and prolong the equipment's lifespan. Proper maintenance practices are essential to avoid discrepancies in experimental results caused by equipment malfunction or wear and tear. Laboratories often adhere to strict maintenance schedules and protocols to ensure the reliability and longevity of their liquid handling systems.
Disadvantages of Liquid Handling
Despite their advantages, liquid handling systems come with challenges. High costs, complexity, and the need for specialized training can be barriers to their adoption. Understanding these disadvantages is crucial for making informed decisions about investing in and implementing these systems in laboratory settings.
Cost and Operational Challenges
Liquid handling systems can be expensive, both in terms of initial investment and ongoing maintenance. The cost of high-end automated systems can be prohibitive for smaller laboratories. Additionally, their operation requires specialized training, adding to the operational costs. Users must be proficient in handling the software and hardware components of a liquid handling system to maximize its potential. However, the benefits in terms of increased throughput, improved accuracy, and reduced errors often justify the investment. Conducting a cost-benefit analysis helps in assessing the long-term value and return on investment of these systems.
Complexity and Training Needs
The complexity of some liquid handling systems can be daunting, particularly for users unfamiliar with this type of advanced laboratory equipment. Automated systems often involve intricate programming and setup procedures that require comprehensive training. Ensuring all personnel are adequately trained is essential to prevent errors, maximize workflow efficiency and, perhaps most importantly, ensure widespread adoption of the technology into the lab. Continuous training and updates are necessary to keep pace with technological advancements and evolving laboratory practices.
In summary, understanding liquid handling systems, their operations, techniques, principles, and associated challenges is essential for optimizing laboratory workflows and enhancing research outcomes. Despite the costs and complexities, the benefits offered by these systems make them indispensable tools in modern science.
Revision: BL-DIG-240520-01 RevB - Understanding Liquid Handling